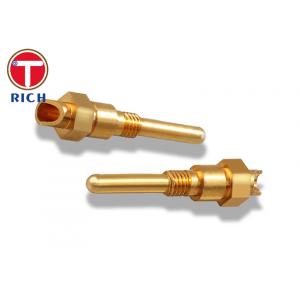
Add to Cart
Brass CNC machining has gained significant popularity in various industries due to its ability to produce precise and complex parts. One particular application where CNC brass parts excel is in the production of copper fiber optic AC/DC pins. In this article, we will explore the material properties of brass, the drawing format required for CNC machining, the production process involved, surface roughness and treatment, and the wide range of applications for these parts.
Brass is an alloy composed primarily of copper and zinc, with additional elements such as lead, tin, or aluminum added to achieve specific properties. This composition makes brass an ideal material for CNC machining as it offers excellent machinability, corrosion resistance, electrical conductivity, and thermal conductivity. These characteristics are crucial for copper fiber optic AC/DC pins, where precision, durability, and electrical performance are paramount.
To manufacture CNC brass parts for copper fiber optic AC/DC pins, precise specifications are necessary. The drawing format should include detailed dimensions, tolerances, material specifications, and any specific surface finish requirements. Computer-aided design (CAD) software is commonly used to create these drawings, ensuring accurate and standardized information for the machining process.
CNC machining is the preferred method for producing brass parts for copper fiber optic AC/DC pins due to its high precision and efficiency. The process involves the following steps:
Design and Programming: The initial step is to create a 3D model of the part using CAD software. The model serves as the basis for generating the CNC program, which contains instructions for the machining equipment.
Material Selection and Preparation: Brass stock material is selected based on the required dimensions and specifications. The stock is prepared by cutting it into the appropriate size and shape for CNC machining.
CNC Machining: The prepared brass stock is clamped onto the CNC machine, which uses computer-controlled movements to precisely remove material according to the programmed instructions. This process includes milling, drilling, turning, and other machining operations to shape the part accurately.
Quality Assurance: After machining, the produced parts undergo rigorous quality checks to ensure they meet the required dimensions, tolerances, and surface finish. This may involve measurements using precision instruments and visual inspection.
Surface Treatment: Depending on the application and aesthetic requirements, the CNC brass parts may undergo surface treatment processes such as polishing, plating, or coating. These treatments enhance the part's appearance, protect against corrosion, or provide additional functionality.
Surface roughness plays a crucial role in the performance and appearance of CNC brass parts. The desired surface finish is typically specified in the drawing format. The CNC machining process itself produces a certain level of roughness, which can be further refined through post-processing techniques like sanding, buffing, or polishing. The choice of surface treatment, such as plating or coating, can also contribute to improving the surface finish and enhancing the part's durability and appearance.
CNC brass parts for copper fiber optic AC/DC pins find application in a variety of industries, including:
Telecommunications: Copper fiber optic AC/DC pins are essential components in fiber optic connectors used for high-speed data transmission in telecommunications networks.
Electronics: These parts are utilized in electronic devices, such as switches, connectors, and sockets, where reliable electrical connections are critical.
Automotive: CNC brass parts play a vital role in automotive applications, including electrical systems, connectors, and sensors.
Aerospace: Copper fiber optic AC/DC pins are employed in aerospace equipment, where they ensure reliable communication and power transmission in avionics systems.
Medical Devices: CNC brass parts are used in medical equipment, such as diagnostic devices, surgical instruments, and imaging systems, due to their biocompatibility and electrical conductivity.
Products Display
Production Process
Our Workshop
Quality Control Standards
To consistently exceed customer expectations, quality control and assurance is achieved through
• Comprehensive written procedures and policies
• Detailed records of incoming raw material
• Optional XRF analysis reports
• Analysis of root cause of non-conformances
• Fully equipped inspection department
• Consistent calibration and labeling of inspection tools
• Designated areas for non-conformationg parts
• Staff members being strongly encouraged to suggest improvements in methods, materials and suppliers
Why choose TORICH?
1. Manufacturer, Exporting and Trading for over 20 years' experiences.
2. Good connection with 1st hand manufacturers engineer and production team directly.
3. TOP A raw material supplier for long term and stable cooperation.
4. Experienced engineers in the field for over 20 years.
5. 7x24hours prompt reply after receiving 1st enquiry.
Packing and Transportation
FAQ